A MORE DETAILED LOOK AT THE PROCESS
Quotes and authorizations
Each
insurance company has its own rules and procedures. The first step is for a
customer to lodge a claim with their insurer, the insurance will advise the
customer on how to proceed. Very often the insurance will do its own quote at a
drive in centre, they may however request that the customer gets a quote or
quotes.
It is important to note that the customer has the right to have his
vehicle repaired where he prefers, provided that the repairer of his choice is
on the insurance panel. If the repairer is not on the insurance panel it is
still possible to insist that the vehicle be repaired at that repairer, but the
process may take slightly longer, with the number of approvals mini/Maxi
Panelbeaters has it is seldom a problem.
Assessment and quotation
Quotes are prepared on the TMS management System and there are four people who can do the
assessment. Our reception is run by 2 very capable ladies, who welcome customers and assist them with
getting a quote. Some quotes may take a little longer due to parts prices that need to be obtained.
Should the customer be in a hurry the quote can be faxed or emailed to them, but should they wish to
wait, they can enjoy a complimentary cup of coffee from our coffee bar.
Authorizations
When the insurance authorizes the claim, it is communicated to us. We then promptly communicate
with the customer to book the vehicle in at the customer’s convenience and an estimation of repair time
is also communicated to the customer at that point. When a vehicle is booked in a comprehensive
check list is done and the customer has the opportunity to study the quote and ensure that all the
expected repairs are on the quote.
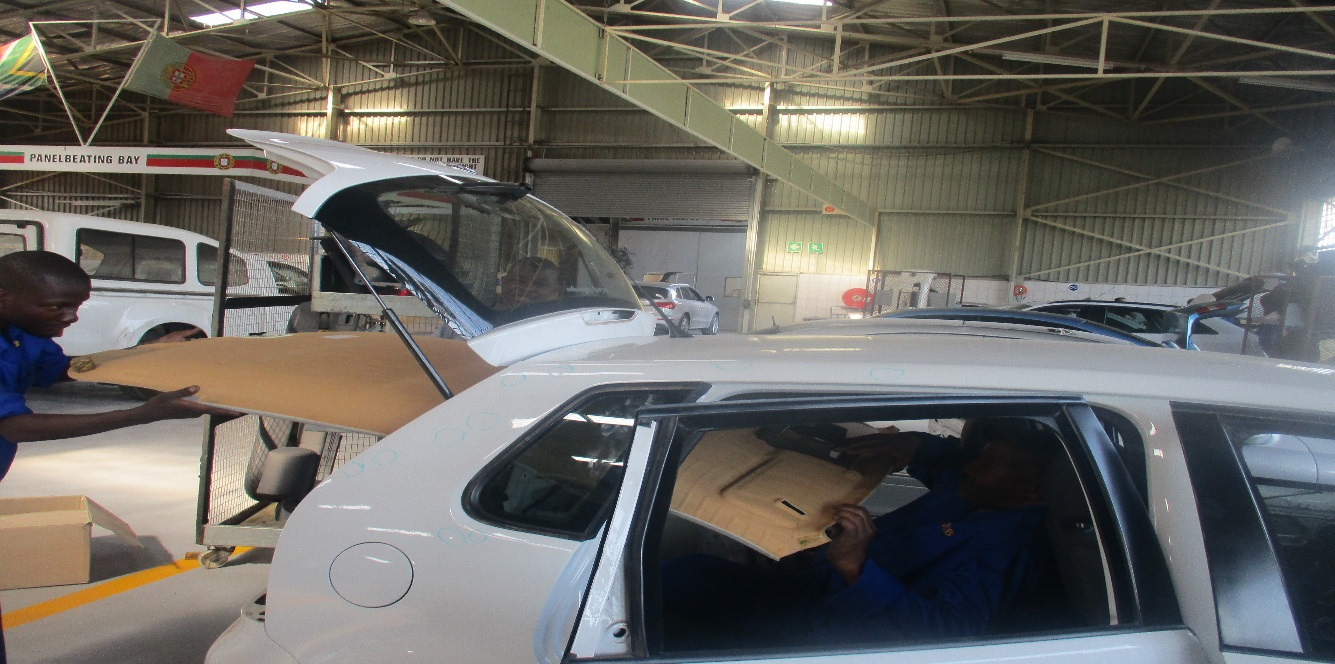
STRIPPING
There are 6 strip & assemble bays with 6 assemblers employed. Striped spares are carefully packed into cages and safely stored in order to avoid damage. Assemblers are sent to all new model training courses that are offered.
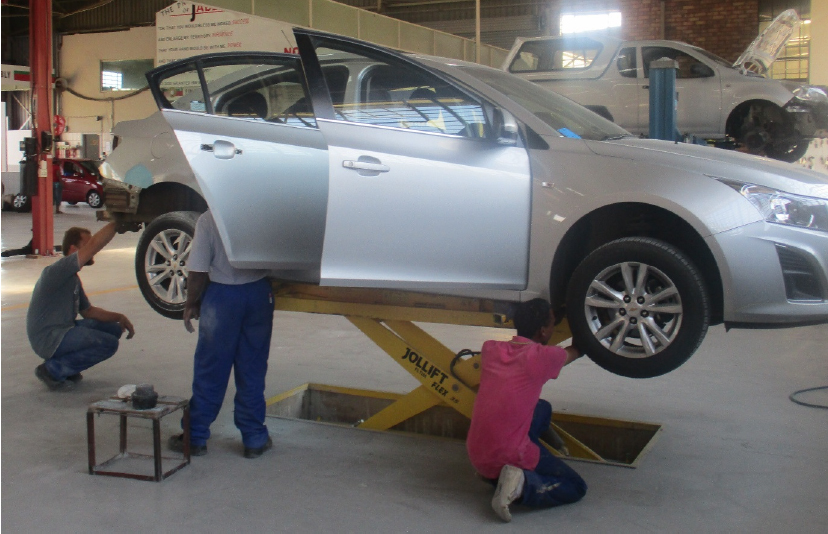
PANELBEATING
We currently have 4 qualified panelbeaters and 4 assistants. We use a Cellete jig for chassis repairs and
Speed benches for smaller jobs.
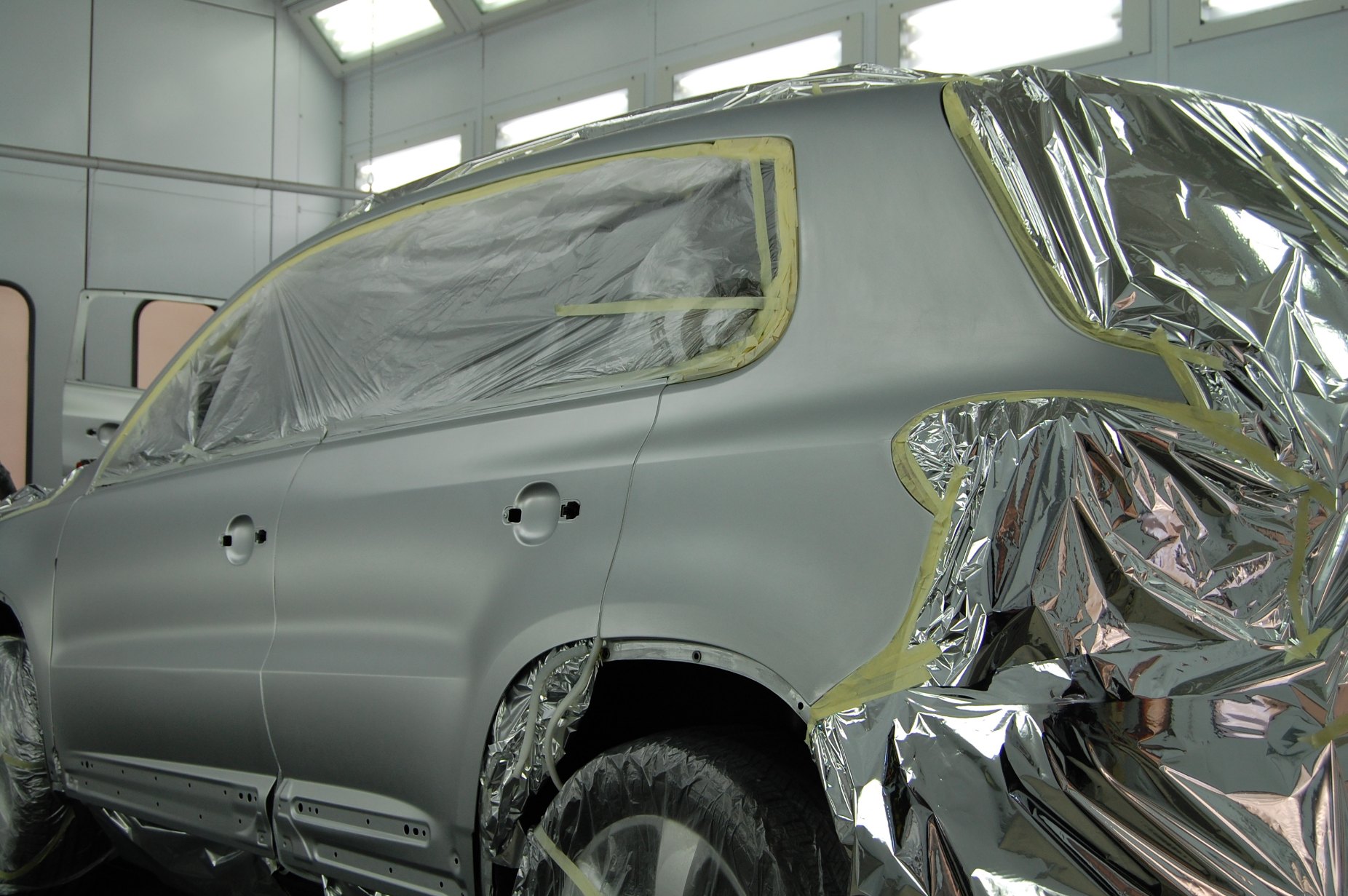
PRIMER
We have 4 primer bays. All employees in the paint shop receive continual on the job training from our paint supplier to use the products correctly.
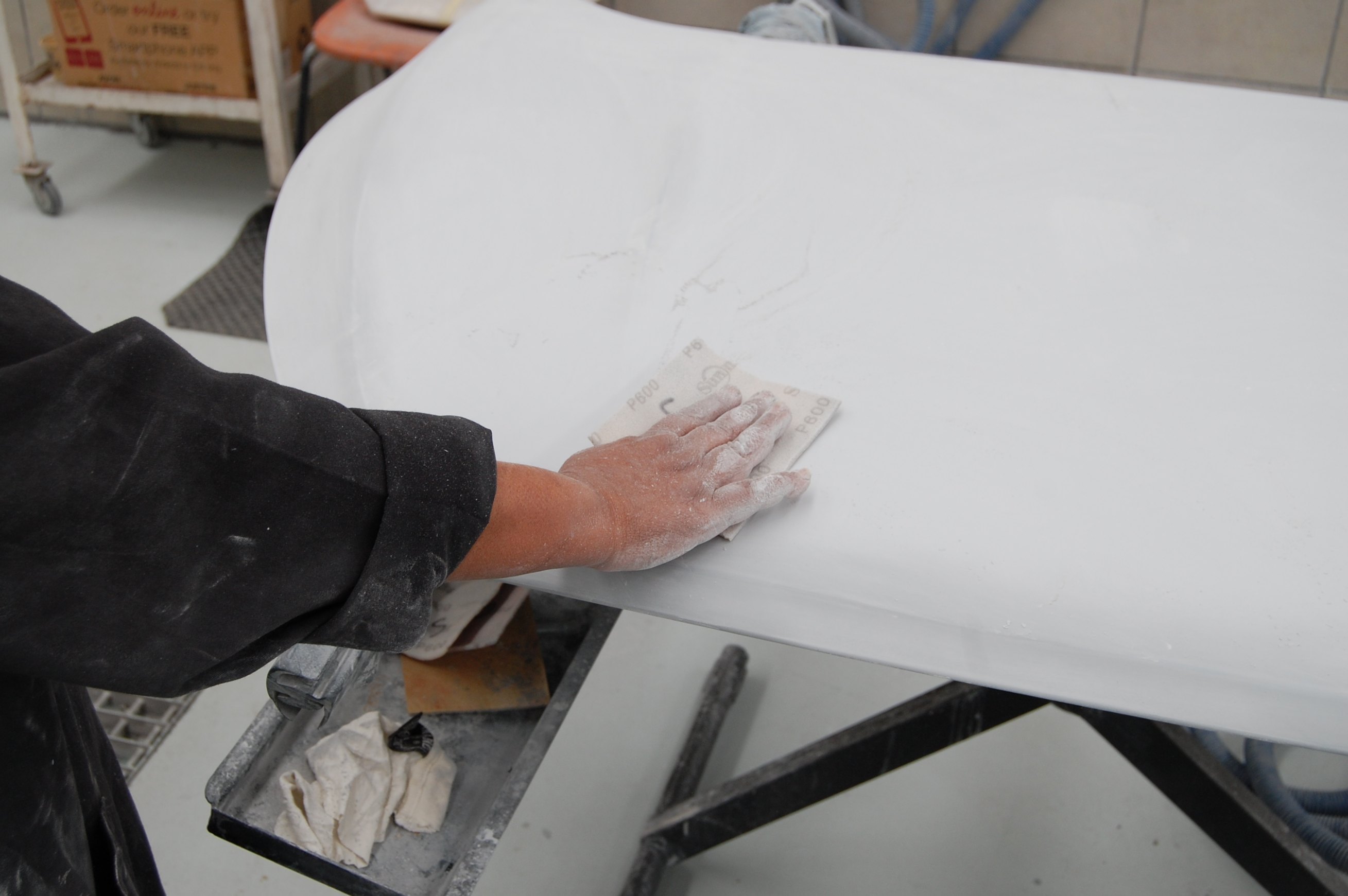
Preparation
We have 5 preparation bays, each with under floor filtration. A dry flatting process is used.
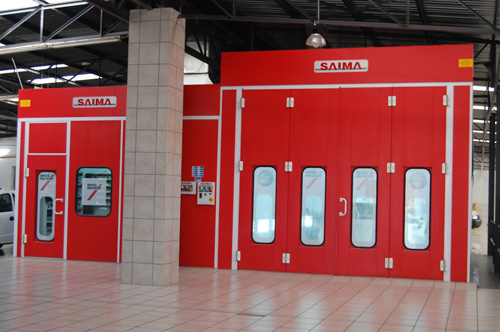
SPRAY PAINTING
We have 2 qualified spraypainters and use 3 spray booth ovens. Waterborne paint from Sikkens is
used. Our spraypainters attend regular courses to stay up to date with the newest techniques and
developments ensuring that they deliver the correct colours with exceptional quality.
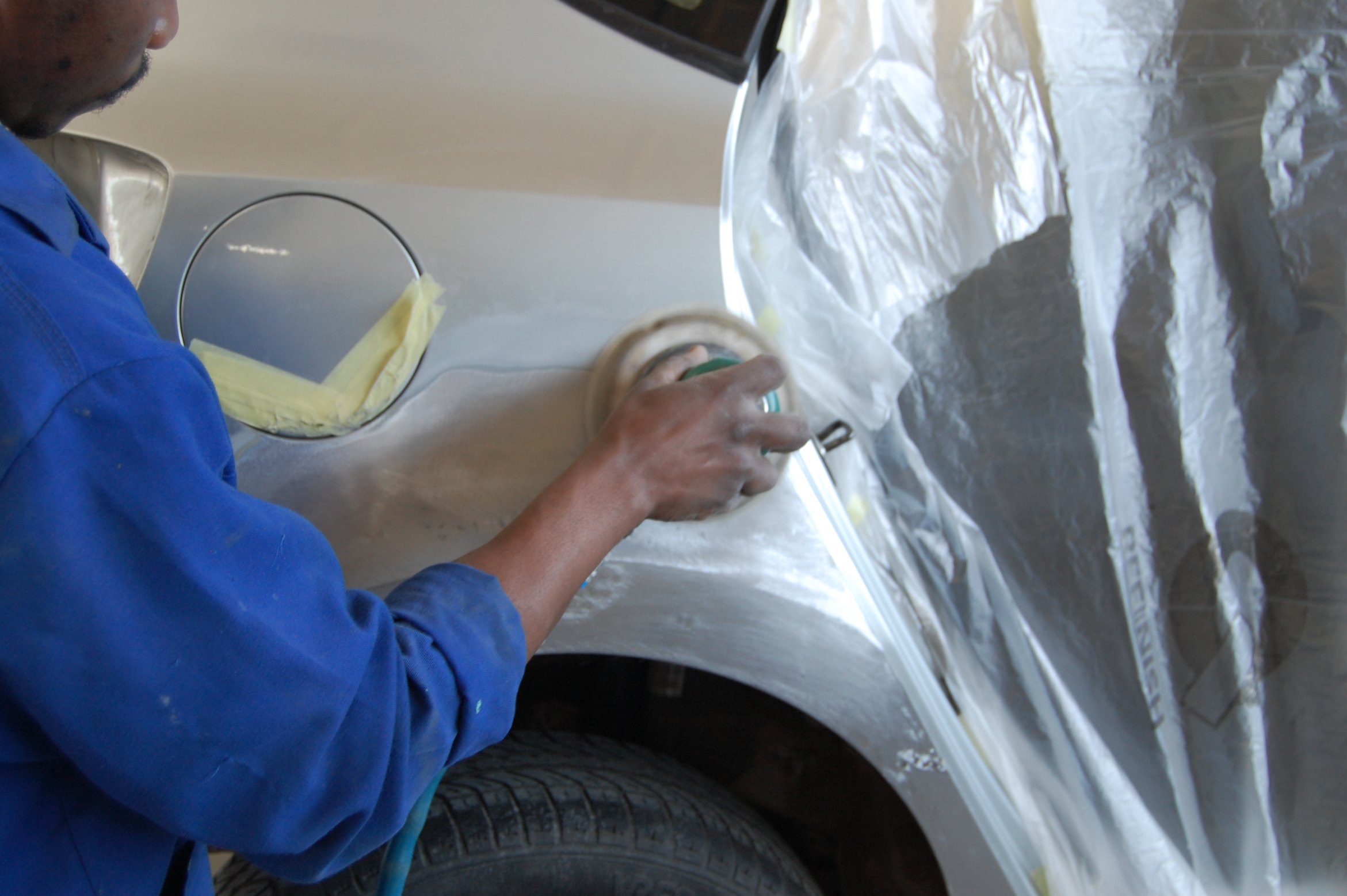
POLISHING
There are 2 polishing bays, both with lifts to ensure that the job gets done properly. Vehicles are quality
checked at this point to ensure that the paint shop has completed its job properly.
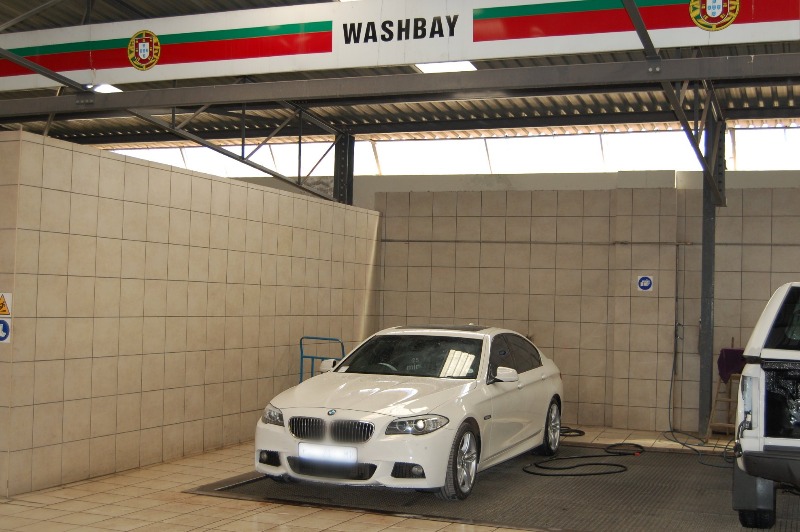
CLEANING
Once assembled vehicles are meticulously cleaned.
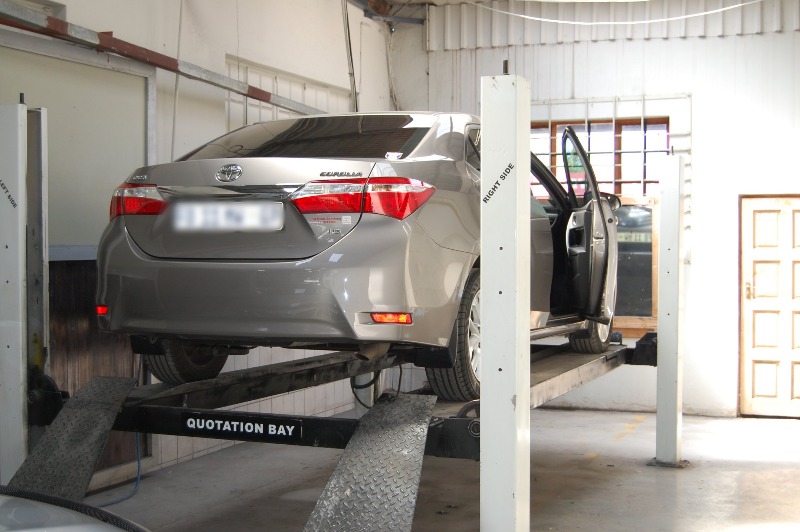
QUALITY CONTROL
When all the work is done, quality of workmanship is checked on a lift. It is ensured that the vehicle will
be to the customer’s satisfaction.
DELIVERY
COLLECTION
Once signed off by Quality Control, the customer is contacted
immediately and informed that the vehicle is ready for collection. The excess amount if any is confirmed and is
payable on collection. When the customer arrives he is given the opportunity to inspect the vehicle
before taking delivery..
GUARANTEES
We take pride in our services
and quality workmanship :
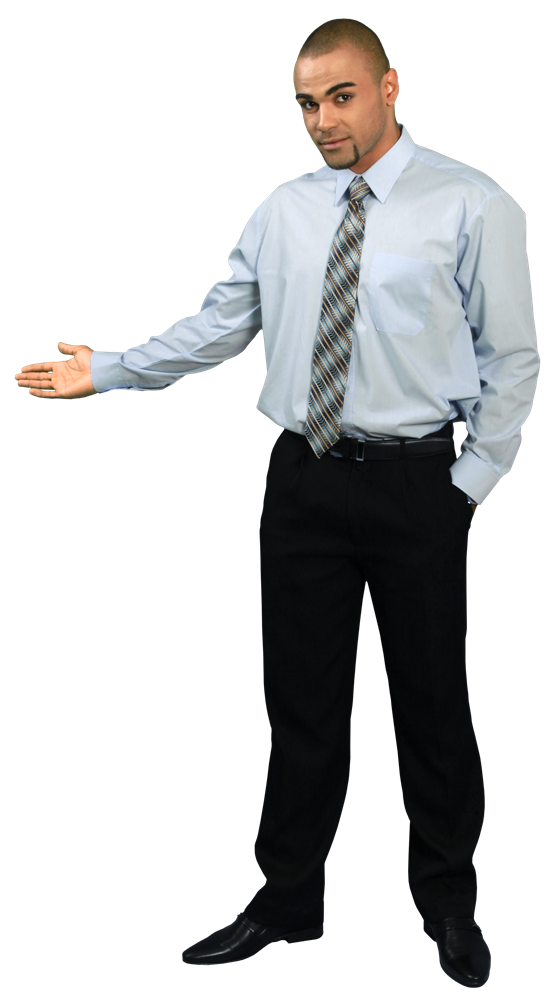
WORKMANSHIP
All work performed shall be free of defects in material and workmanship for a period equal to the outstanding new Manufacturer’s body warranty or 24 months if the new body warranty has lapsed.
PAINT
Warranty as per supplier’s documentation. – Top Coat
PAINTWORK
All paintwork is free from defects and has a warranty period of 3 years